Suppressors represent one of the most fascinating intersections of metallurgical engineering and shooting sports technology. The interaction between high-pressure gases, extreme temperatures, and various metal substrates creates a complex environment that demands careful material selection. In this comprehensive analysis, we’ll explore how different metals perform in suppressor applications, examining their unique properties, advantages, and limitations.
The Basics of Suppressor Metallurgy
At its core, a suppressor must withstand thousands of rapid pressure and temperature cycles while maintaining structural integrity. The primary metals used in modern suppressor baffle construction include stainless steel, titanium, aluminum, and various exotic alloys. Each material brings its own set of characteristics to the table, from thermal conductivity to corrosion resistance, ultimately affecting both performance and longevity.
Stainless Steel: The Industry Standard
Stainless steel remains the benchmark material for suppressor construction, particularly grades like 17-4 PH and 316L. These alloys offer exceptional durability and heat resistance, making them ideal for high-volume shooting applications. The density of stainless steel helps absorb vibration and reduce first-round pop, while its corrosion resistance ensures longevity even in adverse conditions. However, the material’s weight can be a significant drawback, especially in longer configurations or when mounted on lightweight firearms.
Titanium: The Premium Alternative
Titanium has revolutionized suppressor design by offering strength comparable to steel at roughly half the weight. Grade 5 titanium (Ti-6Al-4V) has become particularly popular for its excellent strength-to-weight ratio and corrosion resistance. The material’s higher heat tolerance compared to aluminum makes it suitable for moderate to heavy use, though it generally commands a premium price point. One interesting characteristic of titanium suppressors is their tendency to develop a distinctive heat-treated patina over time, which many enthusiasts find aesthetically pleasing.
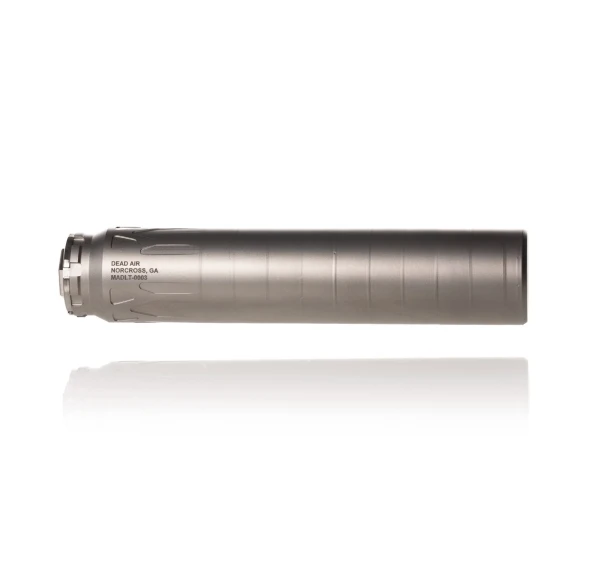
Aluminum: Light Weight Champion
Aluminum suppressors, typically crafted from 7075-T6 or similar aerospace-grade alloys, offer the lightest weight option for shooters. Their excellent thermal conductivity helps dissipate heat quickly, though this comes with limitations on sustained fire capability. Aluminum suppressors, such as the SilencerCo’s Warlock 22, excel in rimfire applications and limited-use centerfire roles, where their weight savings can significantly improve handling characteristics. However, their lower melting point and reduced erosion resistance make them less suitable for high-volume or full-auto applications.
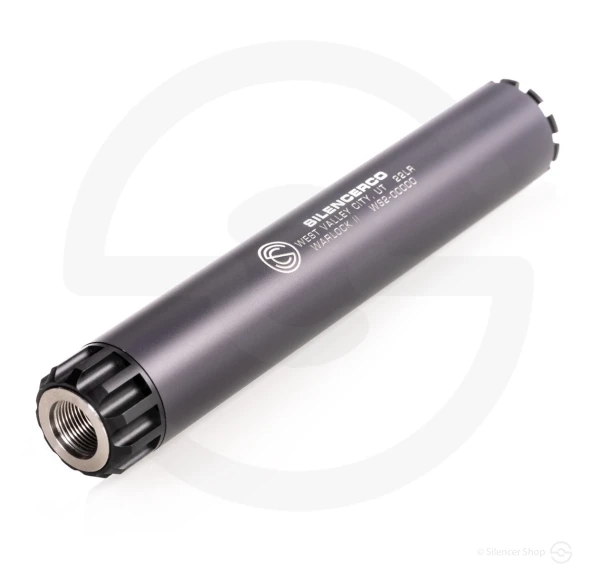
Inconel: The Heavy-Duty Performer
Inconel, a nickel-chromium superalloy, represents the premium end of suppressor metallurgy. This material offers exceptional strength and heat resistance, making it ideal for extreme-use scenarios and full-auto applications. While expensive and challenging to machine, Inconel’s ability to maintain structural integrity under sustained high-temperature conditions makes it invaluable for certain military and commercial applications where reliability is paramount.
Material Combinations and Hybrid Designs
Modern suppressor manufacturers increasingly utilize multiple metals within single designs to optimize performance characteristics. For example, a titanium tube might be paired with stainless steel baffles to balance weight savings with durability in high-wear areas. The CGS Helios QD, constructed of durable 718 Inconel and 17-4 stainless steel, is specifically designed for 5.56 mm rifles and carbines. These hybrid designs represent some of the most innovative approaches to suppressor construction, though they often require sophisticated manufacturing techniques to ensure proper material interface and thermal expansion compatibility.
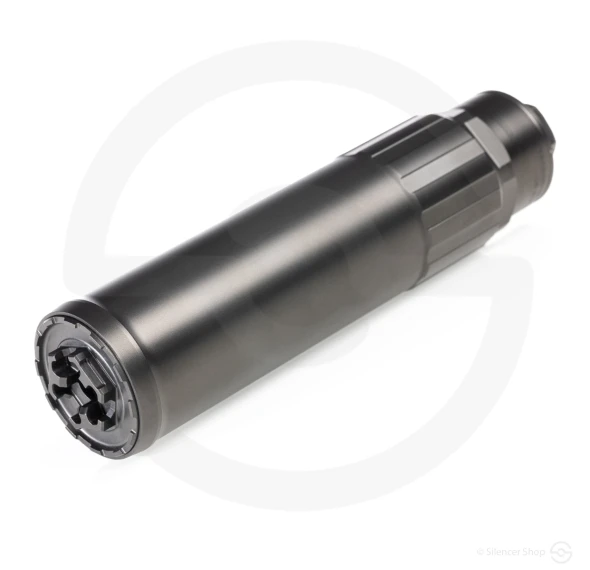
Thermal Considerations and Material Selection
The role of thermal management in suppressor design cannot be overstated. Different metals exhibit varying rates of thermal expansion and heat dissipation, directly affecting both performance and longevity. Stainless steel, for instance, tends to retain heat longer than aluminum but can withstand higher temperatures without degradation. Understanding these thermal characteristics is crucial for both manufacturers and end-users in selecting appropriate materials for specific applications.
Corrosion and Environmental Factors
Environmental resistance plays a crucial role in suppressor longevity. Marine environments, in particular, can be extremely challenging for certain metals. Titanium and high-grade stainless steels generally offer superior corrosion resistance, while aluminum requires more careful maintenance to prevent oxidation. The choice of material must, therefore, consider not only operational requirements but also the intended operating environment.
Manufacturing Considerations
The machinability and weldability of different metals significantly impact both production costs and design possibilities. Titanium, while offering excellent performance characteristics, requires specialized tooling and expertise to machine effectively. Stainless steel provides a more forgiving manufacturing process, while aluminum’s ease of machining helps keep production costs lower. These manufacturing considerations directly influence market availability and price points across different suppressor designs.
Future Trends in Suppressor Metallurgy
The suppressor industry continues to evolve with new material innovations and manufacturing techniques. Advanced coating technologies, novel alloy combinations, and improved manufacturing processes are expanding the possibilities for suppressor design. The ongoing development of new materials and treatment processes suggests that future suppressors may offer even better combinations of weight, durability, and performance characteristics.
Wrap Up
The choice of metals in suppressor construction represents a careful balance of multiple factors including weight, durability, thermal management, and cost.
While no single material provides a perfect solution for all applications, understanding the characteristics and limitations of each option helps manufacturers and end-users make informed decisions based on their specific needs.
As metallurgical science continues to advance, we can expect to see even more innovative approaches to suppressor design and construction, further pushing the boundaries of what’s possible in sound suppression technology.
Read the full article here
Leave a Reply